Эта вакансия уже завершена
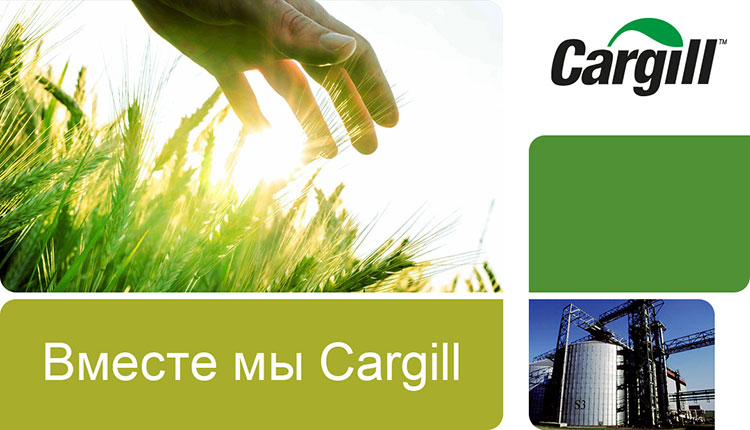
Position Purpose & Summary
- To manage inland silo (90 kMt storage capacity) located in Kutsovka, Kirovohrad region, Ukraine within all applicable laws and procedures while meeting or exceeding location, enterprise and corporate objectives.
- The scope of accountability includes but not limited to production employees, contractor employees, company assets, relations with local communities and authorities.
- This position will provide leadership, technical knowledge and operational experience towards achieving EHS, process safety, food/feed safety and quality of handled products, costs and operating efficiencies, smart capital spending, highly engaged and high performing employees, while serving customer needs equal to, or better than the best across the industry
- This position is finally responsible for all KPIs specific and applicable to the site.
RESPONSIBILITIES:
20% RISK MANAGEMENT
- Provide safety leadership to create and continuously improve safe environment at site for all employees, contractors and visitors. Lead silo team to identify hazards with strong focus on SIF exposure, define and implement appropriate defense layers and controls, and verify that these are effective.
- At site level execute on Cargill EHS, Food Safety programs, strategic initiatives and Calls-To-Action
- Jointly with FSQR function meet quality specifications, Food/Feed safety for grains and seeds handled at site. Handle customer complaints and quality issues
- Champion facility security program to protect people, assets and other property related to the site
- Ensure compliance with all applicable national regulatory and corporate policy & procedure requirements. Ensure all necessary permits to operate are in place and current.
- Bild and maintain trustful environment within the team to ensure proper reporting of all incidents, Near Miss conditions/situations or other undesired events
- Lead incidents investigations including root cause analysis on all EHS incidents of the defined magnitude. Be accountable for proper Corrective Actions planning and followed up on regular basis
20% OPERATIONAL EFFECTIVENESS
- Prepare and manage the operational budget of the silo. Track expenditures in each area, make appropriate adjustment to costs control to meet expectation of the bottom-line PL result.
- Monitor sourcing process for all supplies, goods and services. Approve purchase orders in line with defined magnitude. Collaborate with regional procurement team to streamline procurement process, achieve best cost of ownership for the assets, low operational cost and to enlarge share of preferred suppliers.
- Drive Yield improvements (TCY and Dry base shrink)
- Provide high level of cooperation with Commercial and Supply chain functions to appropriately adjust day-to-day operational plans
- Create an annual plan for silo, set goals and priorities. This include operational budget, base capex plan, location performance goals and targeted KPIs based on the country/functional/Enterprise regional business plan. Regular follow-up on site performance with all relevant stakeholders is essential
20% CONTINUOUS IMPROVEMENT
- Demonstrate adherence and champion Continuous Improvement process. Be able to identify opportunities and challenge the current state. Pursue improvements with good discipline in execution and establish a culture where data drives decision making and the team focuses on continuous improvement across all areas (safety, maintenance, efficiency, etc.)
- Deploying innovative and new technology and automation to create more efficient operations to minimize production cost and maximize profitability. Stay current on latest technology development by maintaining contact with other Cargill facilities, experts, suppliers etc.
20% TALENT AND INDIVIDUAL PERFORMANCE MANAGEMENT
- Align business needs with individual motivations and aspirations to set effective Performance goals. Explore how to stretch goals to the right level of challenge while keeping goals refreshed and relevant (иметь план замещения, проводить ассесмент)
- Drive High Performance of all silo employees by using Performance Management Process and having ongoing courageous conversations to increase engagement and productivity of silo employees. Personally demonstrate power of using recognition and constructive feedback to set employees up for success. Implement personal Performance Improvement plans where needed to set employee back on track.
- Develop and keep updated Succession Plan. Identify qualification gaps and development needs.
10% CAPITAL EFFECTIVENESS
- Create and regular update 5-year rolling base capital investment and capitalized replacement plan.
- Use MyPPM system to manage project portfolio of the site and execute on particular projects in line with Project Delivery Process depending on project magnitude.
10% OTHER
- Support relations with silo customers/local farmers.
- Manage relations with local communities and authority.
- Execute on charity projects in the region
REQUIREMENTS:
Education
- Higher education/University degree in Process Technology/Mechanical/Engineering or other relevant specialties
Experience
- 5-7 years in a Managerial position in bulk material handling (preferably grain handling) facility
- General commercial awareness
Skills
- Strong communication and influencing skills
- Good understanding of CI, change management tools
- Analytical and problem-solving. Understanding Root Cause Analysis (RCA) tool.
- Capability to search, compile and digest information, analyze data for decision making
- Ability to lead multi-disciplinary teams and projects. Teamworking
- Organization, time management, prioritizing and the ability to handle a complex, varied workload
- A good knowledge of IT packages including general computer technology, Microsoft office apps, plant systems (1C, Savigent, general understanding of SCADA), internet and web based apps/systems
- English both verbal and written (not a must but highly preferred)